FDM (fused deposition modeling) printers create objects by heating filament and depositing plastic layer by layer along paths.
FDM printers are ideal for rapid prototyping, large objects, and fun trinkets. FDM printers are good for first time makers looking to get into 3D printing.
MSLA (masked stereolithography) printers create objects by selectively curing photopolymer resin layer by layer with UV (ultraviolet) light.
Resin printers are ideal for high-detail objects (like miniatures), complex geometry, batch printing, and creating molds. They are straightforward to operate, but the cleaning process and safety concerns demand more attention.
Table of Contents
Should I Use FDM or Resin?
When to use Resin:
- High-detail
- Complex geometry
- High-temperature parts
- Batch printing small parts
- Creating molds for jewelry casting etc.
When to use FDM:
- Large prints
- Quick, low-cost prints
- Ultra-stiff parts
- Low-density parts
- Minimize safety concerns
Quality of FDM vs Resin
FDM Quality
FDM 3D prints are best known for their visible layer lines. These layer lines can be minimized by using smaller layer heights, printing at higher temperatures, sanding the print, and using chemicals to smooth the surface (e.g. acetone on ABS or ASA).
Stringing can also be a common issue, but it can be minimized by adjusting slicer settings.
Resin Quality
Resin 3D prints are best known for their high-detail and translucency, with no layer lines. However, the supports for a resin print can leave small craters throughout the print. These can be minimized by avoiding heavy supports or fixed in post-processing.
When exposed to sunlight, clear resin prints can yellow over time, but this degradation can be prevented with protective coatings.
The FDM miniatures above were printed on a Prusa MK3S+ with the default quality settings and Hatchbox PLA. This showcases what your smaller filament prints will look like starting off. While the settings can be optimized to reduce issues such as stringing, it is nearly impossible to completely eliminate some quality defects associated with FDM printers.
The resin miniature was printed using Siraya Tech Simple Smoky Black with the resin default of 0.05 mm layer height. Resin printers can use a layer height of 0.01 mm but even the default provides an amazing level of detail. On the resin miniature's hand, you can see webbing between the fingers - this is caused by overexposure and is easily fixed by reducing the exposure time per layer.
Filament vs Resin 3D Printer Cost
FDM Printers
If you're a newcomer to the world of 3D printing, we suggest starting with a printer like the Sovol SV06. These user-friendly printers arrive mostly pre-assembled, feature a direct drive extruder, and employ an induction probe for auto-leveling. With decent quality control and these convenient features, you'll be up and running in no time. This class of FDM printer generally start at $200.
Direct drive printers can use materials such as PLA, PETG, PP, OBC, and TPU right out of the box. The printers shown below all use an all-metal hotend, which means you can print ABS, ASA, HIPS, Nylon, and PC.
The size of the printer is a significant factor in determining its price. Most budget FDM printers have a build volume close to 220x220x250 mm. If you're looking for affordable large printers, consider the SV06 Plus or Neptune 4 Max.
The Voron is a project printer that costs around $1,000. Bambu printers like the X1-C bring additional features and ease of use.
Elegoo Neptune 4 Pro
$300
($10 Off)
Assembly: Partial
Extruder: Direct Drive
Auto-Leveling: Yes
Max Nozzle Temp: 300°C
Max Bed Temp: 110°C
Print Volume: 225mm (L) 225mm (W) 265mm (H)
Neptune 4 vs 4 Pro
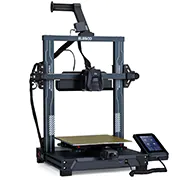
Sovol SV06
$210
Assembly: Partial
Extruder: Direct Drive
Auto-Leveling: Yes
Max Nozzle Temp: 300°C
Max Bed Temp: 100°C
Print Volume: 220mm (L) 220mm (W) 250mm (H)
SV06 vs SV06 Plus
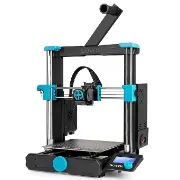
Qidi X-Plus 3
$670
Assembly: Fully
Extruder: Direct Drive
Auto-Leveling: Yes
Max Nozzle Temp: 350°C
Max Bed Temp: 100°C
Print Volume: 280mm (L) 280mm (W) 270mm (H)
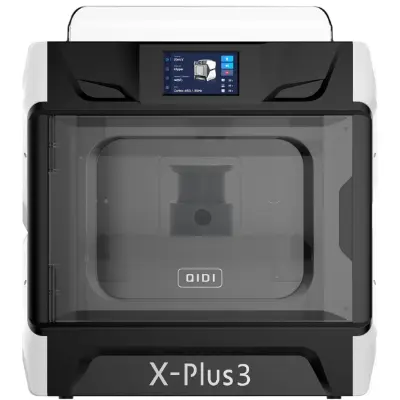
Bambu X1-Carbon
$1,200+
Assembly: Fully
Extruder: Direct Drive
Auto-Leveling: Yes
Max Nozzle Temp: 300°C
Max Bed Temp: 120°C
Print Volume: 256mm (L) 256mm (W) 256mm (H)
Bambu Printers
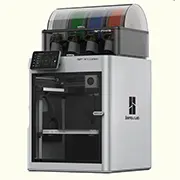
Resin Printers
To get started with 3D printing, it is important to consider the cost of all the equipment you will need, especially when it comes to resin printing. While smaller resin printers like the Mars 4 are cheaper than FDM printers, the overall cost of a resin setup will be higher due to the need for ventilation and cleaning equipment.
For beginners, we recommend starting with a smaller resin printer like the Mars 4 mentioned above. If you require more build volume, then a medium-sized M5S Pro, Saturn 3, or Mighty 8K is ideal. There are large-sized resin printers but they cost over $800, and it is better to start with a smaller printer to learn the entire process.
After printing with resin, post-processing is necessary remove uncured resin from the part. To streamline the cleaning and curing, most people purchase cleaning equipment such as a wash & cure machine or an ultrasonic cleaner, which can add an additional $50-200 to your budget depending on the size you pick.
Additionally, resin printers will require ventilation. The cheapest and most effective form of ventilation will be to place the resin printer outside the home, in a garage or workshop. If the resin printer is indoors, it should be enclosed and vented out a window. Enclosures like a grow tent are easy to setup and will cost $60-200. Larger printers will demand more space.
During the winter, an external heat source often needs to be added to keep the resin at an optimal printing temperature. The minimum printing temperature is 20°C, but it is best to check manufacturer recommendations. Assuming you already have an enclosure, a ceramic heater and temperature controller will only cost $40-50.
Elegoo Mars 4
$250
($10 Off)
Resolution: 0.018mm (XY) 0.01mm (Z)
7" 9k Screen
Print Volume: 153mm (L) 77mm (W) 175mm (H)
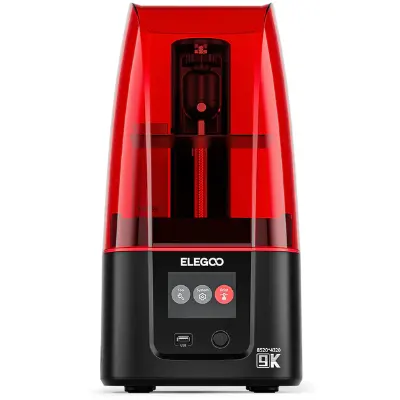
Phrozen Mini 8K S
$350
Resolution: 0.022mm (XY) 0.01mm (Z)
7.1" 8k Screen
Print Volume: 165mm (L) 72mm (W) 170mm (H)
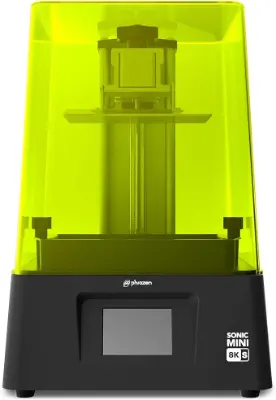
Elegoo Saturn 3
$350
Resolution: 0.019mm (X) 0.024mm (Y)
10" 12k Screen
Print Volume: 219mm (L) 123mm (W) 250mm (H)
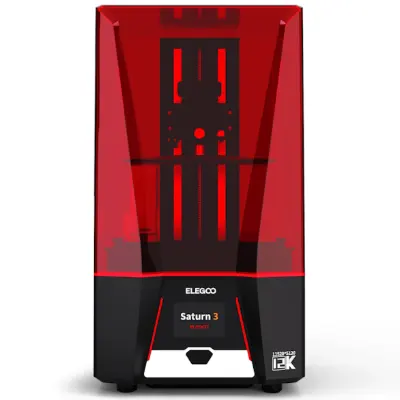
Anycubic Mono M5S Pro
$460
($30 Off)
Resolution: 0.016mm (X) 0.024mm (Y)
10.1" 14K Screen
Print Volume: 223mm (L) 126mm (W) 200mm (H)
M5S Pro vs M5S
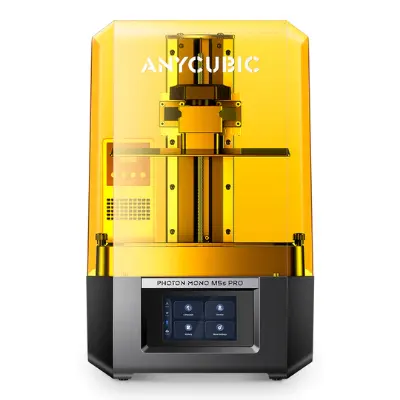
Filament vs Resin Material Cost
Cost of Filament
Entry-level filaments, such as PLA, PETG, and ABS, typically cost between $15 and $30 per kilogram.
Engineering filament, such as PC, Nylon, and ASA, will be $50-100 per kilogram.
Most consumer filament costs no more than $150 for a roll, while industrial filament like PEEK can cost upwards of $500 per kg. You can explore brands, prices, and properties with our filament tables.
Cost of Resin
Budget resin is $20-35 per kilogram, especially with promo codes.
Engineering resin starts at $40 per kg. This would include durable, flexible, and high-temperature resins.
Formlab's SLA resin is $175-300 per kg, and this is the typical price ceiling. The exceptions to this are ceramic and biomedical resin, of which can be up to $500 per kg. You can explore brands, prices, and properties with our resin tables.
Strength & Properties of Filament vs Resin
There's a common misconception that FDM-printed objects are stronger or more durable than those created using resin printing. However, this isn't always the case. Certain resins, like Siraya Tech Sculpt, boast a higher tensile strength compared to PLA and PETG materials. When it comes to durability, Siraya Tech Blu demonstrates a performance quite similar to PETG.
To achieve optimal outcomes, it's crucial to choose a material well-suited for your specific project. For instance, when 3D printing miniatures, it's advisable to opt for a durable resin that can endure frequent handling without breaking. Budget resins are often more fragile and may not be the ideal choice for such applications.
Filament Properties
Basic filaments, such as PLA or PETG, are sufficient for general trinkets and project pieces. However, for specialized applications that require greater strength, stiffness, or temperature resistance, it is common to use filament infused with materials like carbon fiber or glass fiber.
Carbon fiber infused filament allows FDM printed parts to have a high modulus (stiffness). Filament blends like PP-CF (polypropylene) can create highly sought after lightweight, high-strength parts.
Filaments materials like OBC (Olefin Block Copolymers) and TPU (Thermoplastic Polyurethane) excel at flexibility. Filaments and blends made from PETG, PP, ABS, ASA, Nylon, and PC have high tensile strengths and fracture elongations, so parts printed from these filaments will be more durable than PLA or budget resin.
Resin Properties
Most makers turn to resin for printing highly detailed miniatures. These models often contain thin features that are fragile when brittle budget resin is used. When miniatures are printed with a durable resin, they are able to withstand plenty of punishment. Affordable engineering resins such as SuperPP, Blu, Tenacious, or Anycubic Tough can match or exceed the durability of PETG - these are the type of resins you will want to use for impact resistance.
For Resin, the tensile strength and fracture elongation is commonly listed by manufacturers but the Izod test is not. It is used to determine how much energy a material can absorb under high-impact. The Izod test allows us to see that a resin like SuperPP can absorb 120 J/m whereas Anycubic Tough can only absorb 55 J/m.
When you need to print high-temperature components, resin printers are used, unless you have a FDM printer that can print towards and above 300°C. With any resin printer, you can use a high-temperature resin like 3D Material's SuperHDT or Siraya Tech Sculpt to create parts that can withstand up to 240°C.
Filament & Resin Printer Safety
Ultrafine Particles (UFPs) enter the air from sources like 3D printing, cooking, candles, or laser printers. These suspended particles enter our lungs and travel until they reach the alveoli, where they can cross the air-blood barrier. Once they are in our blood, they are distributed throughout our body, damaging cells along the way. Our kidneys and intestines are the two primary organs that filter out UFPs.
Visit our 3D Printing Air Quality Roundup to get extensive up-to-date safety information and guidance.
FDM Safety
- PLA garage or workshop - Ready to print; encouraged to capture UFPs.
- ABS, HIPS, PC, etc garage or workshop - Ready to print; encouraged to vent and capture UFPs.
- PLA indoors - Keep out of bedrooms and use a small air cleaner to capture UFPs.
- ABS, HIPS, PC, etc indoors - Isolate the FDM printer in a separate room and vent out a window if possible; otherwise, use an air cleaner to capture UFPs and VOCs.
3D printing with PLA is considered the safest option available. However, when you begin working with materials such as PETG, ABS, Nylon, and others, it's essential to take extra precautions.
At the very least, an air cleaner should be positioned near the printer. This air cleaner should be equipped with a high MERV (13-16) or HEPA filter to capture nanoplastics and, ideally, carbon granules to handle VOCs. If feasible, situating the printer outside your living space (garage or workshop) can greatly reduce the need for ventilation or filtration.
Resin Safety
- Resin garage or workshop - Ready to print; recommended to vent.
- Resin indoors - Isolate the resin printer in a separate room and vent out a window. Filtration should only be used as mitigation.
Ideally, resin printers should be placed outside the residence (garage, shed, or balcony) but they can be indoors in a separate and sealed room if they are being vented out a window.
Filtration can be used as mitigation and a secondary defense. Using an enclosure like a grow tent will increase the efficiency of ventilation, and it helps keep the heat in for when the temperature drops below 20°C. A small temperature controlled heater is a reliable method to keep the resin up to the optimal printing temperature.
When interacting with the resin printer you should wear disposable or reusable nitrile gloves, and it is a best practice to wear eye and clothing protection. If you get any resin on your skin, wash it off with soap and water as soon as possible - do not use IPA. You can visit our FAQ page to find more safety guidelines and tips.
Disclaimer: You assume all responsibility and risk for the use of, but not limited to, the resources, advice, and opinions of 4D Filtration or its employees. 4D Filtration or its employees do not assume any liability or create any warranty for the use of any information. 4D Filtration may receive commissions for referral links. Prices are approximated for simplicity and they may fluctuate due to sales or markdowns. Amazon .com should refer you to your local amazon site if you are not in the United States; there is a chance Amazon's link redirect system will take you to a different product.